With the word “steels” we refer to all those steels that, thanks to their chemical and structural composition, can be subject of heat treatment in order to guarantee the required mechanical characteristics.
Heat treatments are operations that modify steels' structure through the temperature variations, which are well established in a precise period of time and have a controlled cooling to achieve the desired mechanical characteristics.
Treatment cycles are chosen on the basis of the following desired characteristics: hardness, impact strength, machinability.
In order to accomplish a correct heat treatment, it is fundamental to know the critical points or transformation points of each steel, which indicate the structural change depending on the temperature variation.
Steel's critical points depend mainly on chemical analysis and carbon content.
The most important ones are:
- Ac1 = temperature at which, during the heating, austenite's transformation begins (approximately from 700° C to 750°C);
- Ac3 = temperature at which, during the heating, the transformation of ferrite in austenite ends;
- Ms = temperature at which, during the cooling, the transformation of austenite in martensite begins.
There are further critical points, which are less important though, so we won't write them on the list.
Heat treatments can be divided into preliminary and final ones.
Preliminary ones are useful to confer steel those characteristics that will improve following mechanical machining (cutting, machinability for machine tools, limitation of deformations at the next heat treatment).
Final ones are carried out on finished pieces in order to acquire the desired mechanical characteristics.
The most common preliminary heat treatments are:
- STRESS RELIEVING: heat treatment that leads to heating and the continuity of a sufficient temperature, followed by an appropriate cooling, for the purpose of lowering internal tensions without modifying the structure;
- NORMALIZATION: heat treatment that leads to an austenitizing temperature, followed by a cooling in calm air;
- ANNEALING: heat treatment that leads to heating and the continuity of a sufficient temperature, followed by a cooling in such conditions that steel, after going back to room temperature, will find itself in a structural state that is closer to the stable equilibrium state. There are the following types of annealing:
- full annealing: annealing at a temperature that is higher than Ac3;
- sub-critical annealing: annealing at a temperature that is slightly lower than Ac1;
- isothermal annealing: annealing that leads to austenitizing temperature followed by a cooling that is interrupted by the continuity of a temperature at which austenite transforms completely in ferrite-perlite (black and white structure);
- spheroidizing annealing: annealing that generally leads to an extended continuity at a temperature that is close to Ac1 in order to cause steel spheroidization.
The most common final heat treatments are:
- CASE-HARDENING: heat treatment to which steel, which is at austenitic state, is submitted (austenitizing temperature), in order to achieve a superficial enrichment of carbon. Case hardening can be preceded by adequate preliminary treatments for the purpose of reducing deformations and it has to be followed by heat treatments among which one is hardening, which will confer the required superficial harden, and the other one is stress relieving.
- HARDENING: heat treatment that has the purpose of achieving precise mechanical characteristics. It concerns a heating at hardening temperature or austenitizing temperature, followed by a controlled coolng apt to achieve a transformation for what regards the structure from austenite to martensite and potentially bainite.
- DRAWING TEMPER: heat treatment at which a steel is submitted that has already suffered a harden either through hardening or through another heat treatment, so that its properties can be brought to the desired level.
- QUENCHING AND TEMPERING: treatment that concerns harden through hardening followed by a drawing temper at an elevated temperature. It has the purpose of achieving the combination between mechanical characteristics and, particularly, a good ductility and toughness.
- STRESS RELIEVING: heat treatment that leads to heating and a continuity at a sufficient temperature, followed by an appropriate cooling, with the purpose of reducing internal strains without modifying the structure.
- SUPERFICIAL HARDENING: treatment of harden at which steel is submitted, which is heated at a temperature higher than Ac3, so it is submitted to a rapid controlled cooling. The treatment can also concern only some parts of the considered piece and the superficial heating is an induction heating. Superficial hardening is generally preceded by a preliminary treatment (annealing, normalization, reclamation) and it has to be followed by stress relieving.
- NITRIDE HARDENING: thermochemical treatment at which steel is submitted for the purpose of achieving a superficial enrichment of nitrogen that confers an elevated superficial hardness (HV 550-950), with a superficial layer of more or less mm 10.
HARDENABILITY
In order to satisfy the desired mechanical characteristics, all special steels have to be submitted to heat treatments.
The most common heat treatment is hardening + drawing temper, which causes the transformation from the initial structure, called austenite, to the final structure, reached after the heat treatment and called martensite.
The tensile mechanical characteristics, the toughness and the strength of pieces of steels depend largely on the percentage of martensite obtained after hardening.
Hardenability is a feature of steel that allows to transform austenite in martensite in a decreasing way, from the piece's surface until the heart in function of the cooling speed during the hardening/quenching treatment.
Hardenability depends on the content of carbon and alloying elements, on the dimention of austenitic grain and on the parameters of heat treatment (temperature, time and shutdown tool).
In industrial practise it is satisfying to get at least 50% of martensite at heart of the parts built with quenched and tempered steels, 70% of martensite for case hardening steel, 80% of martensite for spring steel or high-performance steel.
Hardenability is a fundamental feature for the choice of steel, which will be destined to the construction of mechanical pieces whose mechanical characteristics shall be enhanced after the thermal treatment.
Steels' hardenability is evaluated through Jominy test (UNI 3250). With this test, through hardening treatment of a standardized test tube, a curve is obtained, which has a decreasing harden measured from the different distances from the cold extremity of the test tube itself.
All steels, in function of chemical analysis, are classified with the hardenability curve Jominy, which is indicated in the Uni tables.
ALL OUR STEELS HAVE RESTRICTED, CONTROLLED AND CERTIFIED HARDENABILITY.
CONTROLLED GRAIN STEEL
In order to control grain coarsening, which would be an obstacle for carbon diffusion, a reduction of toughness and an increase of deformations during heat treatments, during the sharpening process of casting small quantities of elements such as aluminium, niobium etc. are added, which impede steel's austenitic grain coarsening.
The quality of steel is higher the finer is austenitic grain. The coarse of austenitic grain is verified with the Mc Quaid-Ehn method according to Uni 3245, which is universally recognized.
The most restrictive specifications consider grain coarse that goes from 5 to 8 or even finer.
ALL OUR STEELS ARE CONTROLLED GRAIN STEEL, CERTIFIED 6 OR EVEN FINER ACCORDING TO MC QUAID-EHN METHOD.
MACHINABILITY
All steels are destined to mechanical processing, which can be more or less complex, with machine tools through a turnings removal system, in order to obtain finished parts. Machinability is a fundamental need for all steels in order to optimize the costs of mechanical processing. Machinability depends on different factors, among which some are metallurgical ones.
The more the steel is alloyed, the higher the resistance and the hardness in the ferrite phase it will be, so steels won't be very machinable.
Moreover, if hardness is excessively low, it can make machinability difficult due to the formation of long turnings.
In order to improve machinability, you can operate in various ways:
- you can operate on the preliminary heat treatment with different annealing, for example machinability annealing, fixing a maximum limit for what concerns hardness, or isothermal annealing to confer steel a defined structure in order to have a controlled hardness within a maximum and minimum limit;
- you can operate on steel's chemical analysis, adding elements that contribute to break the turning during mechanical machinability.
The most efficient elements are the following ones:
- lead is what overall improves machinability. Despite this, it causes a deterioration of mechanical characteristics (especially impact strength) and it is less and less produced because of pollution and ecological problems.
- Sulphur causes the turning to break, even if to a lesser extent comparing to lead. It is added to steel in a quantity that goes from 0.020 to 0.040%, according to the Uni regulation. Moreover, it doesn't cause deterioration of mechanical characteristics.
In order to further improve machinability, some steelworks, after years of research, have elaborated steels with improved machinability through the modification of sulphur, that goes from threadliketo globular, correcting calcium or tellurium during the elaboration of casting. This led to have steels with a machinability that is very close to lead steel, without its negative effects though.
WE HAVE A COMPLETE ASSORTMENT OF SOME QUALITIES OF CASE HARDENING STEELS AND HEAT-TREATABLE STEELS AT AN IMPROVED MACHINABILITY.
For technical in-depth analysis, please go to the section “download”, where you will find the steelwork's technical publications.
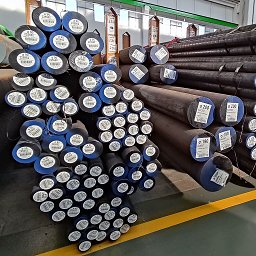
our special steels
M.T.ACCIAI has a large stock of steel always available in stock
Steel that we commercialize comes exclusively from the best steelworks of the European Community.